スプレーコート
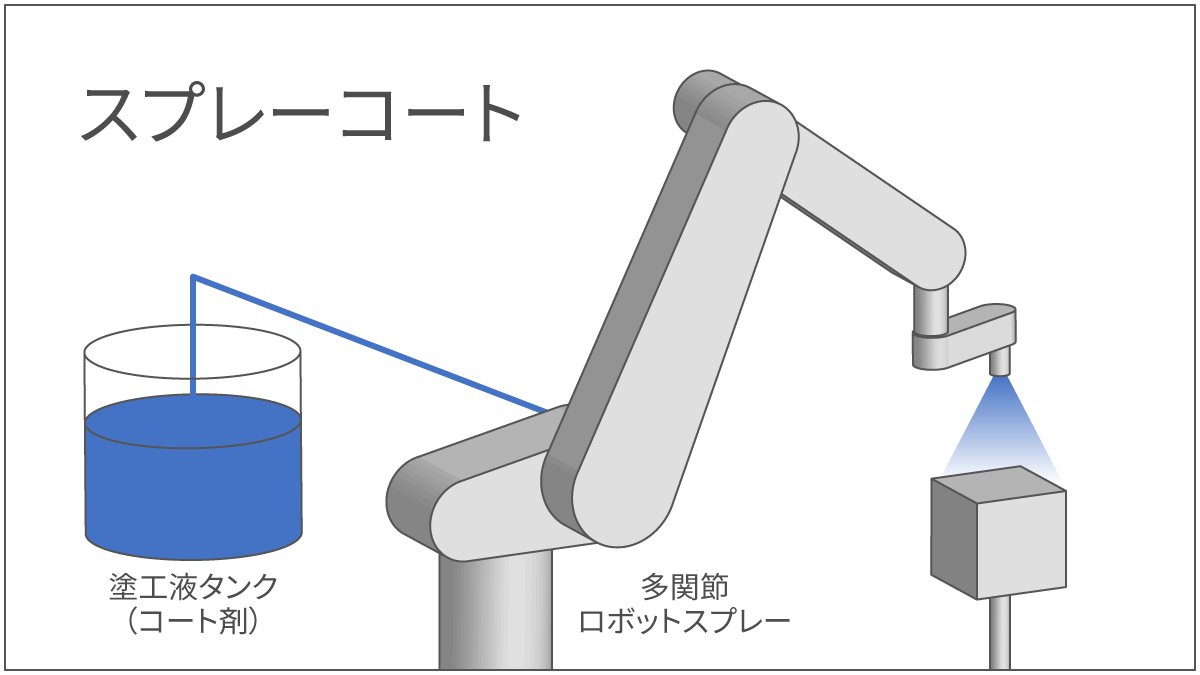
1. スプレーコートとは
スプレーコートとは、液体に高圧をかけて、霧状に噴出させて吹き付ける方法です。
ハードコートを塗工する際によく使用される塗工方法の一つになります。
2. スプレーコートの特長
様々な形状へのコーティング
平面形状だけでなく、成形品などの曲面や複雑な形状でもコーティング可能。
均一な膜厚制御が可能
スプレーガンの移動速度とコート剤の固形分濃度の調整により、均一な膜厚制御が可能。
薄膜から厚膜まで幅広い膜厚を塗工可能
希釈濃度による調整や重ね塗りにより薄膜から厚膜まで幅広い膜厚を狙うことが可能。
3. スプレー方式の種類
スプレー塗工時は、コート液を霧状にする必要があります。
その方法には、エアースプレー方式、超音波スプレー方式、静電スプレー方式などがあり、用途、条件により使われていますが、この3種類の方式について説明します。
エアースプレー方式
汎用性が高く、基材の形状を選ばずに塗工が行えます。
外観良く塗工が行いやすく、コストが比較的安いなどのメリットがあります。
(ニデックのスプレーコート装置は、このエアースプレー方式を用いています。)
超音波スプレー方式
加圧されたエアーではなく、超音波振動によりコート液を微粒子化する方法です。
非常に均一な霧状になり、緻密な膜形成に向いています。
静電スプレー方式
空気圧などで霧化した塗料にマイナス極、被塗布物をプラス極を帯電させることにより電気的に被塗布物に塗布する方法です。
塗布効率が良いことが最大のメリットとなります。
4. スプレー塗工装置の種類
多関節ロボットスプレー
独自にプログラムを組むことにより、様々な形状への塗工が可能です。
特殊な形状など少数を塗工するのに向いています。
(ニデックのスプレーコート装置は、この多関節ロボットスプレー装置となります。)
スピンドルスプレー
塗工対象物を回転させながら、スプレー塗工を行います。
精密なコントロールは難しいですが、大量生産に向いています。
5. スプレーコートの仕組み
スプレーコートによるハードコート塗工の仕組み、手順は以下となります。
STEP1
固形分濃度を調整したコート剤(塗料、薬剤)をタンクに補充し、装置に充填する。
STEP2
対象物表面のクリーニング、マスキングを行った基材を塗工台にセットする。
STEP3
塗工プログラムを選択し、対象物の塗布面に一定の距離と塗工速度を保ちながら、スプレーを吹きかけていく。
STEP4
対象物の表面に均一な薄膜が形成される。
※その後乾燥、硬化工程を経てコーティングは完了です。
6. 塗布速度、固形分と膜厚の関係
スプレーコートによる膜厚は、主にコート剤を吹きかける速度と塗布するハード液の固形分に依存し、一般的に塗工速度が速い場合、薄い膜になり、遅い場合は厚い膜になります。
また、ハード液の固形分が低い場合、薄い膜になり、高い場合は厚い膜になります。
膜厚のコントロールは、主にこれら2種の要素で調整します。
7. スプレーコートの流れ
スプレーコートは、一般的に前処理、洗浄を行った後、乾燥・硬化の後工程を行いますが、一例として、ハードコート加工の流れを以下に説明します。
STEP1 前処理
被塗布物のマスキング処理や、密着性改善処理を行います。
STEP2 洗浄
被塗布物表面のクリーニングを行います。方法としては大きく分けて、ドライプロセスとウェットプロセスの2種類があります。
STEP3 コーティング
スプレーコートを行います。
STEP4 乾燥
コート剤中に含まれる溶剤分を揮発させ、塗膜となる成分のみにします。
STEP5 硬化
UV硬化や加熱硬化など、コート剤に適した硬化方法にて硬化させ完成となります。
8. ニデックのスプレーコート
ニデックでは、自社開発した生産性に優れたUV硬化型のハードコート剤を製造・販売しており、そのコート剤を用いた、スプレーコートの受託対応も行っております。
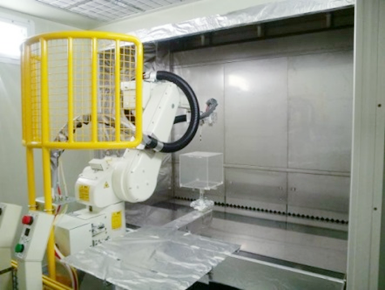
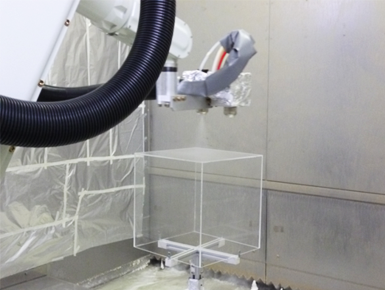
最大加工サイズ | ||
1 | 高さが100 mm以下の場合 | 600×600×100 mm |
2 | 高さが300 mm以下の場合 | 300×300×300 mm |
成形品など様々な形状への塗工が可能です。
お問合せ
コーティング外注先にお困りの際は、お気軽にお問合せフォームからお問合せください。