蒸着とスパッタはどう違う?特徴・仕組みを解説
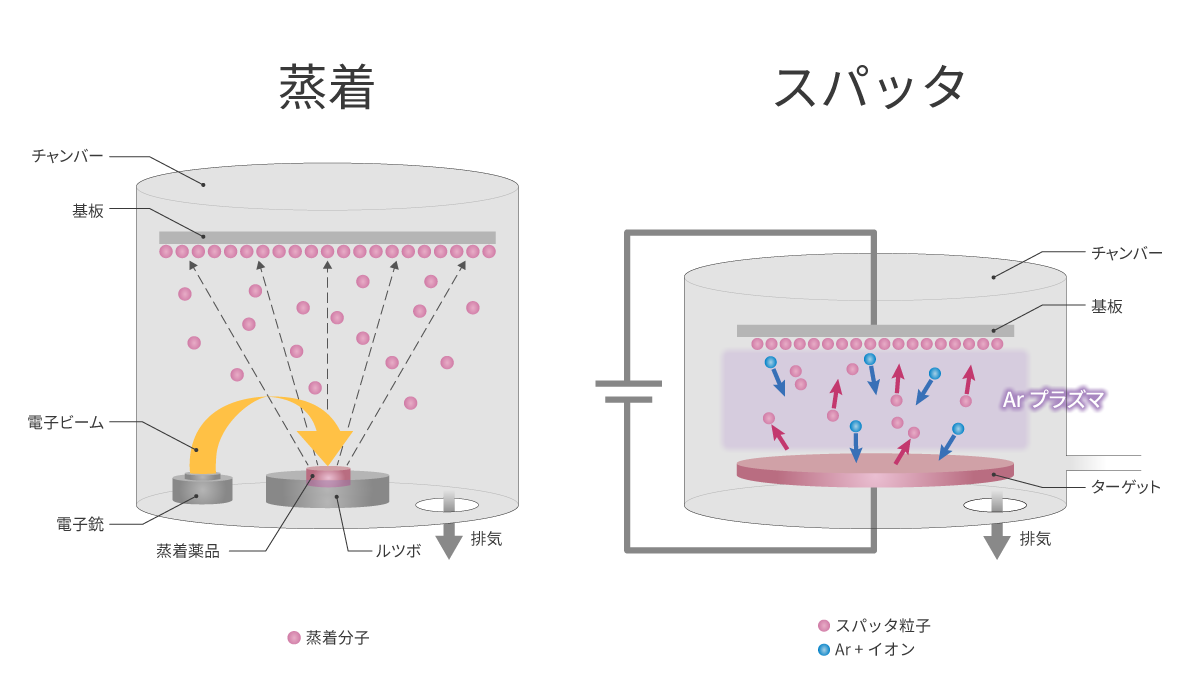
コーティング加工は製品の機能性を高めたり、機能を長く保持させたりする役割を持っています。製品の外側・内側には多くのコーティング技術が使われています。「蒸着」と「スパッタ」はそのなかでも代表的な技術ですが、あまり違いがわからないという人もいるのではないでしょうか。ここでは蒸着とスパッタの基本的な仕組みやコーティング方法を解説し、比較のために参考となる情報をお伝えしていきます。
1. 蒸着とスパッタの仕組みの違い
最初に蒸着とスパッタの概要、原理や仕組みを比較、解説します。
蒸着とは
蒸着は、真空中で物質を蒸発させて成膜する方法です。日本では、1930年代にレンズの反射防止膜の成膜に蒸着が使われるようになったのが始まりで、スパッタより以前から実用化されてきました。光学部品の発展に伴い、蒸着技術も進歩しており、現在では多様な材料に対応しています。蒸着の特徴は、原理がシンプルで理解しやすいという点です。
蒸着の手順を簡単に説明すると、以下の流れとなります。
❶ 原料となる物質(蒸着薬品)と膜をつける対象物(基板)を容器(チャンバー)内に設置する
❷ 容器(チャンバー)内を真空にする
❸ 原料を加熱して蒸発(気化)させる
※コーティング原料の加熱方法は、抵抗加熱式、電子ビーム式、高周波誘導式、レーザー式などがあります。
❹ 気化した原料が膜をつける対象物(基板)に付着し膜を形成する
蒸着の仕組み
スパッタとは
スパッタは、スパッタリング法とも呼ばれています。スパッタリングの本来の意味は、Ar+(アルゴンイオン)のような陽イオンが高速でターゲット(原料)に衝突したとき、ターゲットを構成している粒子が放出される「現象」を指します。スパッタはこの現象を利用し、粒子を一定の並びに堆積させ薄膜形成に応用したものです。
スパッタリングの発見は、1852年と蒸着が活用される以前でした。実用化されたのは米国において、1960年代以降となります。1965年にはスパッタを使った最初の商用電子顕微鏡が作られました。
スパッタの手順を簡単に説明すると、以下の流れとなります。
❶ 原料(ターゲット)と膜をつける対象物(基板)を容器(チャンバー)内に設置する
※この時の距離は蒸着よりも近距離となる
❷ 容器(チャンバー)内を真空にして、不活性ガス(Ar)を導入する
❸ 基板とターゲット間に高電圧を加える
❹ 電子・イオンが高速移動し原料(ターゲット)に衝突するとスパッタリング現象が発生
❺ 原料の粒子を弾き飛ばし、膜をつける対象物(基板)に付着
❻ 薄膜が形成される
スパッタの仕組み
2. 蒸着とスパッタのメリット・デメリット
蒸着とスパッタをさらに比較するために、メリットとデメリットを解説していきます。
蒸着のメリット・デメリット
メリット |
|
デメリット |
|
上記の「抵抗加熱式」とは電気加熱方法の一種で、金属やセラミックスなどに電流を通して電気抵抗で熱を発生させる手法です。融点が高い原料の場合、蒸発気化させるのに数千℃が必要となるため、抵抗加熱式では蒸着ができない為、電子ビーム蒸着を用います。
スパッタのメリット・デメリット
メリット |
|
デメリット |
|
3. 蒸着とスパッタ 選択のポイントは
既述のとおり、蒸着とスパッタでは特徴が異なります。そのため選択には、まず双方のメリットとデメリットを十分に理解しなければなりません。
幅広い用途と低コストの蒸着
一般的には、蒸着の方が、金属・非金属に対応できるなど、用途が広いと言えるでしょう。また、装置や手順がシンプルなので、コストも低く抑えられます。コート完成までの時間が短く、製品が損傷するリスクがないのも魅力です。
高融点金属で安定するスパッタ
一方、スパッタは、大面積でフラットな形状で特殊性のあるものであれば有効な点があります。高融点金属、合金系や化合物を原料にした場合、薄膜の組成が変わらずに成膜されるため、安定して緻密で強いコーティングが可能です。
このように対象物の状態やコスト感、加工時間などを総合的に検討する必要があります。蒸着の弱点をカバーするような効果を付加する、あるいは独自技術によって克服している企業も存在します。コーティングを依頼する際の入念なコートメーカー選びが、満足度の高い仕上がりの決め手となります。
4. 蒸着とスパッタの用途例
蒸着とスパッタには異なる特徴があります。それぞれの具体的な利用法(用途)を紹介します。
蒸着の用途例
|
|
![]() |
![]() |
蒸着は、対象物に与える影響が少なく、コストも抑えられるという点から、非常に多岐にわたる製品に活用されています。光学部品を中心に広く応用されてきましたが、現在では日常品にも使われる身近な技術です。反射防止効果により映り込みを軽減する、化学変化やカビから守る、また、金属的な演出(装飾ミラー)をするといった活用法も見られます。お菓子の袋にも蒸着によるコーティングが使われており、その際は薄膜が油分や糖分の変質を防ぐ役割を果たします。
スパッタの用途例
|
|
スパッタは、蒸着と比べるとやや応用されている範囲が特殊となります。蒸着では難しい組成比が変化しないコーティング用途に使用される場合が多く、コストも高くなる傾向があります。また、成膜時間が長いということも、コーティングの種類によっては検討する要素となります。
自動車業界やエネルギー関連、光学機器、電子デバイスなどが中心となり、最近では高級家具や高額の装飾品類にも応用されています。スパッタを選択する際には、「スパッタでなければ要望する効果が得られない」という結論が導き出されるか、しっかりと見極めて進めていきましょう。
5. 用途に応じて最適な選択を
蒸着とスパッタは、コーティングの代表的な手法です。それぞれに特徴がありメリットとデメリットもあります。一般的には蒸着の方がシンプルな原理でリスクも少なく、汎用性が高いためさまざまな分野に幅広く使われていますが、コーティングを施したい製品によって選択は異なります。判断が難しい場合は専門のコートメーカーに相談し、自社にとってより良い選択をしていきましょう。
6. お問合せ
蒸着とスパッタについて、わからないことや相談したいことなどございましたら、お気軽にお問合せください。弊社で検討の上、ご要望に適したご提案をさせていただきます。
蒸着の基本や弊社蒸着設備など、蒸着についてさらに知りたい場合は、こちらのページもご覧ください。
※全ての画像はイメージです。